Modular construction to boom
- Tracecost Editorial Team
- Jan 21, 2020
- 2 min read
One red-hot trend that has captured the imagination of investors, developers and other real estate stakeholders is modular construction. Essentially, modular construction refers to the off-site construction of several key components of a structure, a trend that is poised for continued and rapid growth. Installation of the prefabricated sections is completed on site. Prefabricated sections are sometimes placed using a crane. The modules can be placed side-by-side, end-to-end, or stacked, allowing a variety of configurations and styles.
Modular construction has plethora of benefits over conventional construction. Modular construction reduces waste and site disturbance compared to site-built structures. The controlled environment of the factory allows for more accurate construction while allowing the extra materials to be recycled in-house. Also assembly is independent of weather, which can increase work efficiency and avoids damaged building material.
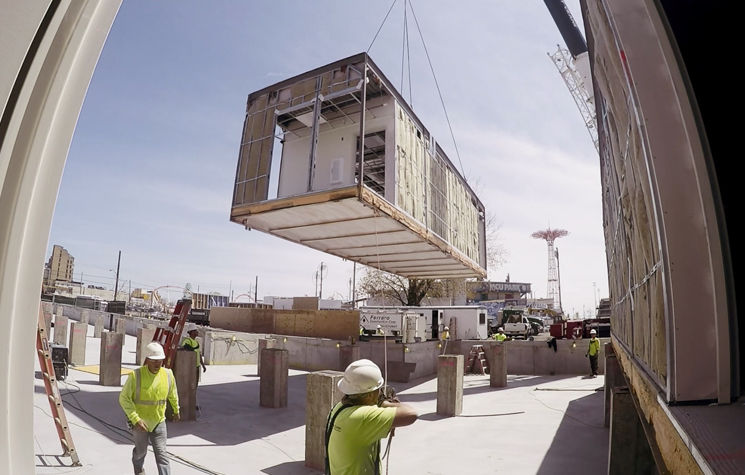
The impact of technology on the construction industry is especially evident in modular. Factory-made steel modules outfitted with the latest electrical and plumbing systems and even high-end finishes and facades can now be transported and then stacked on-site with remarkable precision, often in less time than traditional construction would take.
The application of evolving technologies allows for extremely accurate measurements that practically eliminate the often substantial margin of error that is ever-present with more traditional construction methodologies. Modular construction may also lead to less reliance on highly skilled workers which serves to lower the risk of human error while simultaneously reducing labour costs. The potential list of cost-saving benefits that attach to modular construction is long, and it means more attractive opportunities for the clients that real estate brokers aim to serve.
Well, the modular method has gained a very strong foothold in low-rise housing projects as well as in hotel construction. The projects also have a faster completion time, which means that multifamily units and hotel rooms will begin streaming revenue sooner, a valued metric that is of strong interest to capital investors.
Modular homes are designed to be stronger than traditional homes by, for example, replacing nails with screws, adding glue to joints, and using 8–10% more lumber than conventional housing. This is to help the modules maintain their structural integrity as they are transported on trucks to the construction site.
Recapitulating, modular construction has an edge over traditional construction method. When the modules are prefabricated they are transported to site ready to ‘plug and play’ into the main building. This leaves only localised finishes and vertical and horizontal service reticulation through the communal areas to complete, simplifying the need for on-site trades and significantly shortening construction time. Modular homes tend to be cheaper and quicker to build, as crews are familiar with assembly methods. Some modular homes can even be moved from location to location as owners follow employment opportunities or seek new neighbourhood environments.
Comments